Pipe Stress Analysis is essential to eliminating long-term challenges for piping systems. Our software, Triflex, helps ensure we design the best configuration every time. Subject Matter Expert, Jake Gunelson, provides insight into this valuable resource.
What is pipe stress analysis?
Pipe stress analysis examines a piping system to determine the forces, deflection, and stresses of the pipe and its components, such as supports, anchors, or equipment.
We care about pipe stress analysis because as pipes expand, they create forces that must be within the allowable limits of each system component. For example, let’s say we have a 200-foot-long pipe in a straight line that operates at 200 degrees. While the pipe will be at room temperature when the system is off, it will expand and create forces in the system as it warms up to operating temperature. The good news is that we can mitigate the impact of these forces by starting with pipe stress analysis and understanding the pipe forces and deflections.
What tools do we use for our analysis?
The primary tool that we use is Triflex software. After determining the preliminary routing of the piping system, you can go into the software and input the location of the anchors, pipe routing, support distances, and operating temperature. When you run the software, it will calculate how much movement you’ll experience at any given point and the force placed on the anchors. Then, we relay the force placed on each anchor to the structural engineer, who will properly design the connection to the building structure.
Triflex is also an excellent resource for code compliance. It will generate reports to ensure the system meets building codes and serves as an excellent final check to verify that we are designing piping systems within their capabilities.
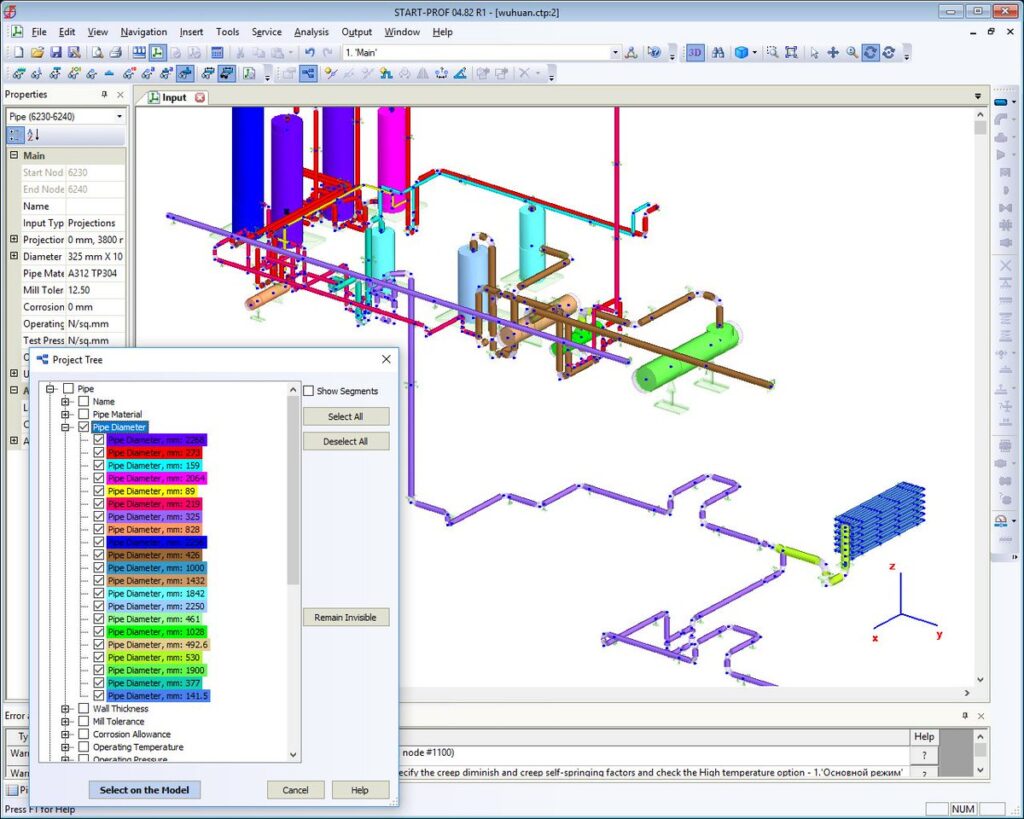
When would we use this on a project?
We would perform pipe stress analysis on any piping system that uses a fluid or gas and is subject to temperature changes. At MCE, we primarily work with steam, water, and glycol solutions in copper and steel piping systems. However, because different piping materials have different expansion rates, the specific codes we follow can vary.
We also use pipe stress analysis to confirm that there is enough physical space for a pipe to expand into as it warms up. It is not uncommon to have a piping system that experiences three inches or more of expansion at specific points, which can cause damage to the structure, supports, or equipment if there isn’t clear space available for the pipe to expand into. Because we can’t stop a pipe from expanding, we need to dictate the exact location where it will expand.
The most common strategy that we use to control where a pipe expands is to put in a U-shaped pipe expansion loop. If we have a section that we know will expand 3 inches, we can build these U-shaped loops to absorb the expansion safely. As both outer sides of the U-shaped loop move and expand, the inner portion will flex, acting as a buffer area to absorb the expansion.
What are the benefits to our clients?
Pipe stress analysis is one of those behind-the-scenes things we do to ensure that our clients receive the right products and a quality piping system design. Ultimately, this helps eliminate any long-term challenges for piping systems and provides peace of mind for our clients.
For our larger projects, such as campuses and airports, we often need to route piping in utility tunnels that are old, tight, and awkward spaces that often don’t have space for a typical U-shaped loop. In these situations, we will use other types of expansion compensation devices and rely heavily on the software.
Our usual process is to pick a spot for an expansion compensation device and run tests to see if it works. If the forces are too much, we choose a different location and rerun the tests until we find an ideal configuration. With Triflex software, we can use this trial-and-error process to find a suitable design for our clients.